Advanced Manufacturing Equipment at DSL
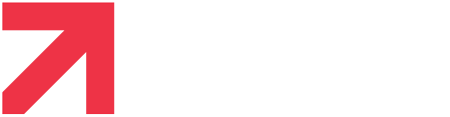
Innovative SMT Line for Optimal Efficiency
DSL employs cutting-edge equipment to consistently deliver competitive, reliable, and robust PCB assemblies. Our fully automated Surface Mount Technology (SMT) line is a marvel of modern manufacturing. It seamlessly guides PCBs through each stage of production via a continuous conveyor system, with each machine intelligently communicating with the next.
This integration ensures the most efficient and high-quality manufacturing process, showcasing DSL’s commitment to technological excellence.
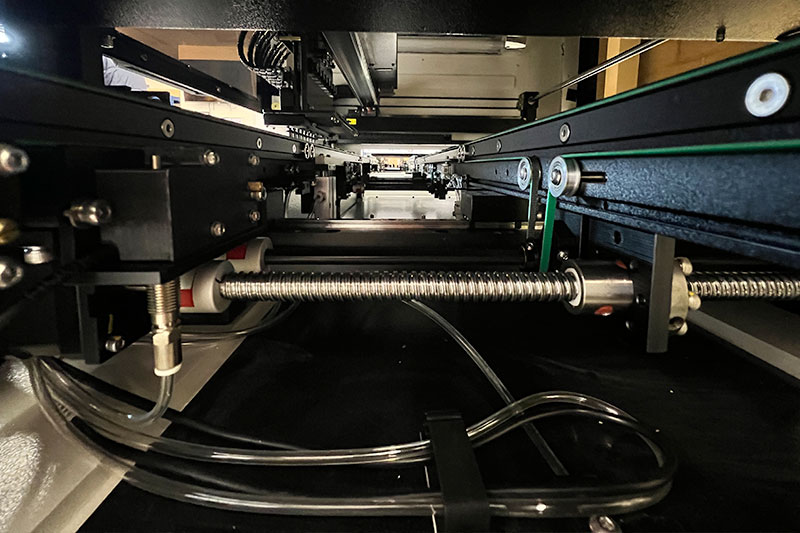
Precision and Quality
DSL’s commitment to quality is evident in our selection of equipment, ranging from basic tools to advanced machinery. We invest in top-of-the-line gear to ensure the highest standards of production – for both our peace of mind and yours.
Our Automatic Stencil Printer revolutionises the way solder paste is applied, automating what was once a tedious manual task. Following this, our dual in-line Pick and Place machines efficiently position tens of thousands of components per hour onto PCBs.
The PCB assemblies then enter our sophisticated 12-phase reflow oven, which meticulously melts the solder paste across different temperature zones for precise component adhesion. Completing the process, a skilled human operator uses a high-accuracy soldering station for through-hole components, followed by a thorough inspection with a 3D automated optical inspection machine, ensuring each assembly meets our stringent quality criteria.
Contact us today
Speak to one of our knowledgeable and experienced team.
Why Clients Choose DSL
DSL’s exceptional client feedback stems from our commitment to quality, innovation, and tailored customer service. Our team’s expertise and dedication ensure reliable electronic manufacturing solutions that meet specific client needs. We prioritise effective communication and support, fostering lasting relationships by delivering consistently high-quality and timely products.
Quality and Innovation
Customised Solutions
Reliable Communication
Customised Solutions
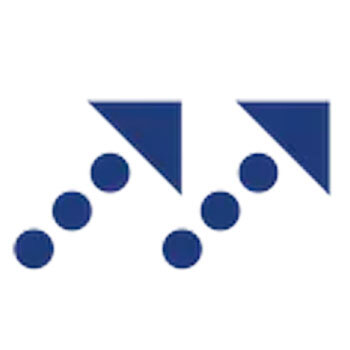
Automated Precision in Solder Paste Application
DSL’s dedication to excellence is highlighted by our use of an Automatic Stencil Printer, a significant upgrade from manual solder paste application. This machine excels in applying solder paste with exceptional accuracy to thousands of pads on a PCB, laying the foundation for reliable circuitry. The automation of this process not only enhances precision but also increases efficiency, allowing for consistent quality across all PCBs.
By automating this crucial step, we ensure that the foundation of each PCB assembly is flawlessly prepared for the subsequent stages of manufacturing, reinforcing our commitment to delivering products of the highest quality.
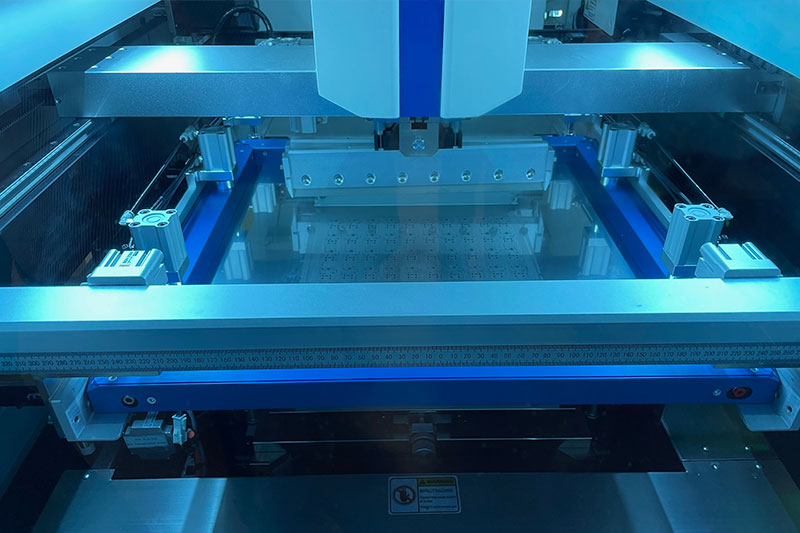
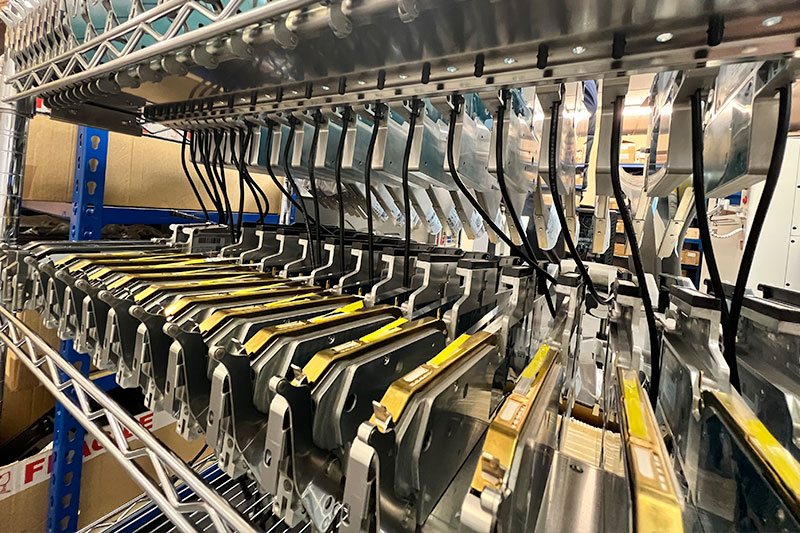
Advanced Component Placement and Reflow Soldering
At the heart of our PCB assembly line are the dual in-line Pick and Place machines. Capable of placing tens of thousands of components per hour, these machines are pivotal in maintaining high productivity while ensuring meticulous accuracy. After component placement, the PCB assemblies undergo a critical soldering phase in our 12-phase reflow oven.
This oven precisely controls temperature across various zones, ensuring optimal melting and adherence of solder paste. This methodical process not only guarantees the secure attachment of components but also maintains the integrity of the PCBs. The combination of high-speed component placement and precision reflow soldering exemplifies DSL’s commitment to harnessing advanced technology for superior manufacturing outcomes.
why choose Dsl
With over 30 years of expertise in electronic design and manufacturing, DSL deeply understands the nuances that differentiate an average Contract Electronics Manufacturer (CEM) from an exceptional one.
Our commitment to excellence is evident in our extended warranties, flexible delivery options, and the presence of on-site experts who are not just adept at designing PCBs but are masters of their craft.
35+ Years of Experience
We’ve been around since Microsoft first released Windows – technology has changed but the core principles of robust electronic design and manufacturing remain the same.
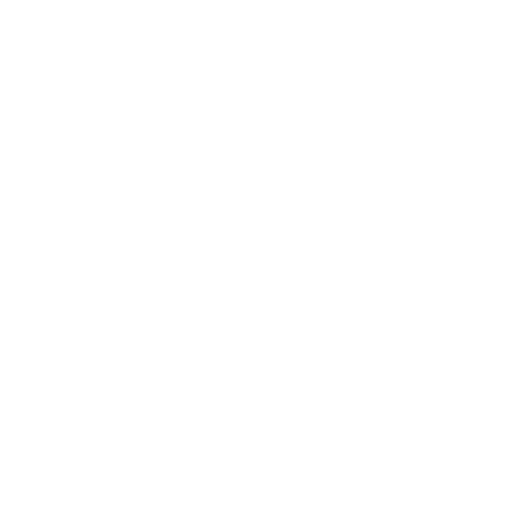
5 Year Warranty
This underpins everything we do as a company, from robust processes, the latest equipment to long term reliable products.
3D AOI
We inspect each PCB assembly with thousands of high definition photos from every conceivable angle to compare to a known good master, all at the push of a button!
Made in Britain
We believe in British manufacturing and so do our clients, the local support, control and quality is tantamount to everything we believe in.
Partnering with DSL for Unmatched Manufacturing Excellence
Choosing to work with DSL means partnering with a leader in PCB assembly, where cutting-edge technology meets expert craftsmanship. Our investment in state-of-the-art equipment, is a testament to our commitment to quality and efficiency.
The meticulous electronic manufacturing processes that we follow underscores our dedication to precision. By collaborating with DSL, you gain access to a manufacturing partner who not only values technological innovation but also prioritises reliability and precision in every project. Our approach ensures that your PCB assemblies are not just products, but that they are crafted to meet the highest standards of the industry.